What is Porosity in Welding: Necessary Tips for Getting Flawless Welds
What is Porosity in Welding: Necessary Tips for Getting Flawless Welds
Blog Article
The Scientific Research Behind Porosity: A Comprehensive Overview for Welders and Fabricators
Understanding the elaborate mechanisms behind porosity in welding is important for welders and producers striving for impeccable craftsmanship. From the composition of the base products to the complexities of the welding procedure itself, a wide range of variables conspire to either exacerbate or alleviate the presence of porosity.
Understanding Porosity in Welding
FIRST SENTENCE:
Examination of porosity in welding discloses vital insights into the stability and top quality of the weld joint. Porosity, characterized by the presence of tooth cavities or voids within the weld steel, is a common issue in welding procedures. These spaces, otherwise properly addressed, can compromise the architectural honesty and mechanical residential or commercial properties of the weld, bring about prospective failures in the completed product.
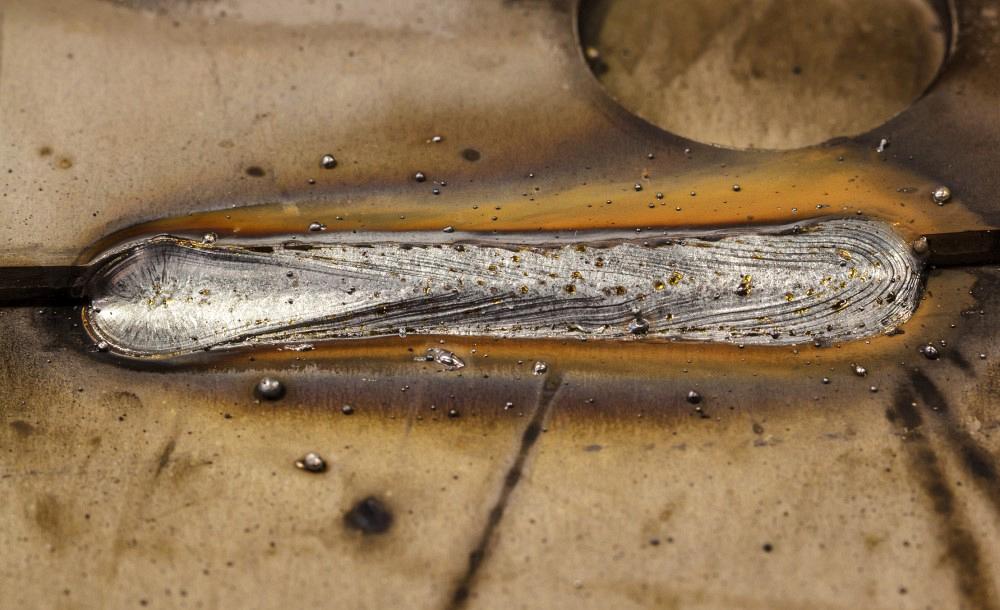
To identify and measure porosity, non-destructive screening methods such as ultrasonic screening or X-ray assessment are usually employed. These methods permit the recognition of internal flaws without endangering the integrity of the weld. By analyzing the size, shape, and circulation of porosity within a weld, welders can make informed decisions to improve their welding processes and attain sounder weld joints.
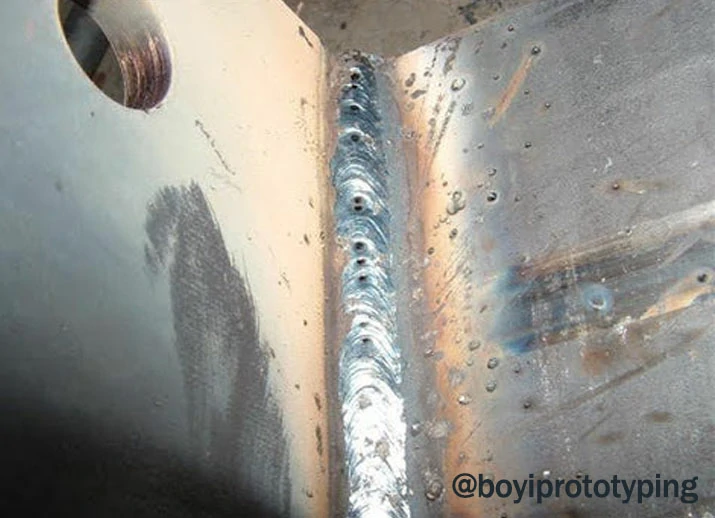
Variables Influencing Porosity Development
The occurrence of porosity in welding is influenced by a myriad of aspects, ranging from gas shielding effectiveness to the details of welding parameter settings. Welding criteria, consisting of voltage, existing, take a trip rate, and electrode type, also influence porosity formation. The welding strategy employed, such as gas metal arc welding (GMAW) or protected steel arc welding (SMAW), can influence porosity formation due to variations in warmth circulation and gas protection - What is Porosity.
Impacts of Porosity on Weld High Quality
Porosity development significantly endangers the architectural stability and mechanical properties of bonded joints. When porosity exists in a weld, it produces gaps or cavities within the product, lowering the general toughness of the joint. These voids serve as stress concentration points, making the weld much more prone to fracturing and failure under load. The presence of porosity likewise damages the weld's resistance to corrosion, as the trapped air or gases within deep spaces can respond with the surrounding atmosphere, causing destruction over time. Additionally, porosity can prevent the weld's ability to withstand pressure or impact, further jeopardizing the general high quality and reliability of the welded structure. In vital applications such as aerospace, vehicle, or architectural building and constructions, where safety and security and longevity are paramount, the browse around these guys harmful impacts of porosity on weld high quality can have serious consequences, emphasizing the importance of minimizing porosity via appropriate welding methods and procedures.
Techniques to Lessen Porosity
In addition, utilizing the appropriate welding specifications, such as the right voltage, existing, and take a trip rate, is important in look at this website protecting against porosity. Maintaining a constant arc size and angle during welding also assists minimize the possibility of porosity.

Making use of the appropriate welding strategy, such as back-stepping or employing a weaving motion, can likewise help distribute warm equally and minimize the chances of porosity development. By implementing these techniques, welders can effectively reduce porosity and generate premium welded joints.
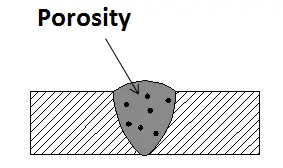
Advanced Solutions for Porosity Control
Applying sophisticated technologies and innovative methods plays an essential duty in attaining remarkable control over porosity in welding procedures. One advanced remedy is using sophisticated gas combinations. Protecting gases like helium or a combination of argon and hydrogen can help in reducing porosity by offering much better arc stability and enhanced gas coverage. Furthermore, using advanced welding strategies such as pulsed MIG welding or changed atmosphere welding can likewise assist mitigate porosity concerns.
An additional advanced option entails the use of advanced welding devices. For example, using devices with integrated functions like waveform control and innovative source of power can enhance weld high quality and minimize porosity dangers. Moreover, the execution of automated welding systems with specific control over criteria can considerably decrease read more porosity issues.
In addition, integrating innovative surveillance and examination modern technologies such as real-time X-ray imaging or automated ultrasonic screening can help in identifying porosity early in the welding procedure, permitting prompt rehabilitative activities. Generally, integrating these advanced remedies can substantially enhance porosity control and improve the general quality of bonded parts.
Final Thought
In conclusion, recognizing the science behind porosity in welding is essential for welders and makers to produce top quality welds - What is Porosity. Advanced services for porosity control can better boost the welding process and make sure a solid and reliable weld.
Report this page